Springback Analysis of AA5754 under Warm Stamping Conditions
DOI:
https://doi.org/10.37256/est.112020104Keywords:
Springback, Analytical model, Warm forming, L-shape bending, Aluminium alloy AA5754Abstract
Prediction of springback has been thoroughly investigated for cold forming processes; however with the rising prominence of lightweight materials and new forming technologies, predicting springback at elevated temperatures has become essential. In this paper, three analytical models and one empirical model were proposed to predict springback of an aluminium alloy AA5754 at warm forming conditions. The analytical models developed were based on the effect of the linear bending moment, uniform bending moment and through-thickness stress gradient respectively on springback, while the empirical model was developed using the results of L-shape bending tests. The model predictions were compared with the experiment results for various forming conditions. At room temperature, all four models had very good agreement. At elevated temperatures, the linear bending moment model was preferred for a die radius of 8mm, whereas empirical and stress gradient models were more suitable for a die radius of 4mm; in both cases, very close agreement was achieved where errors were within 5%.
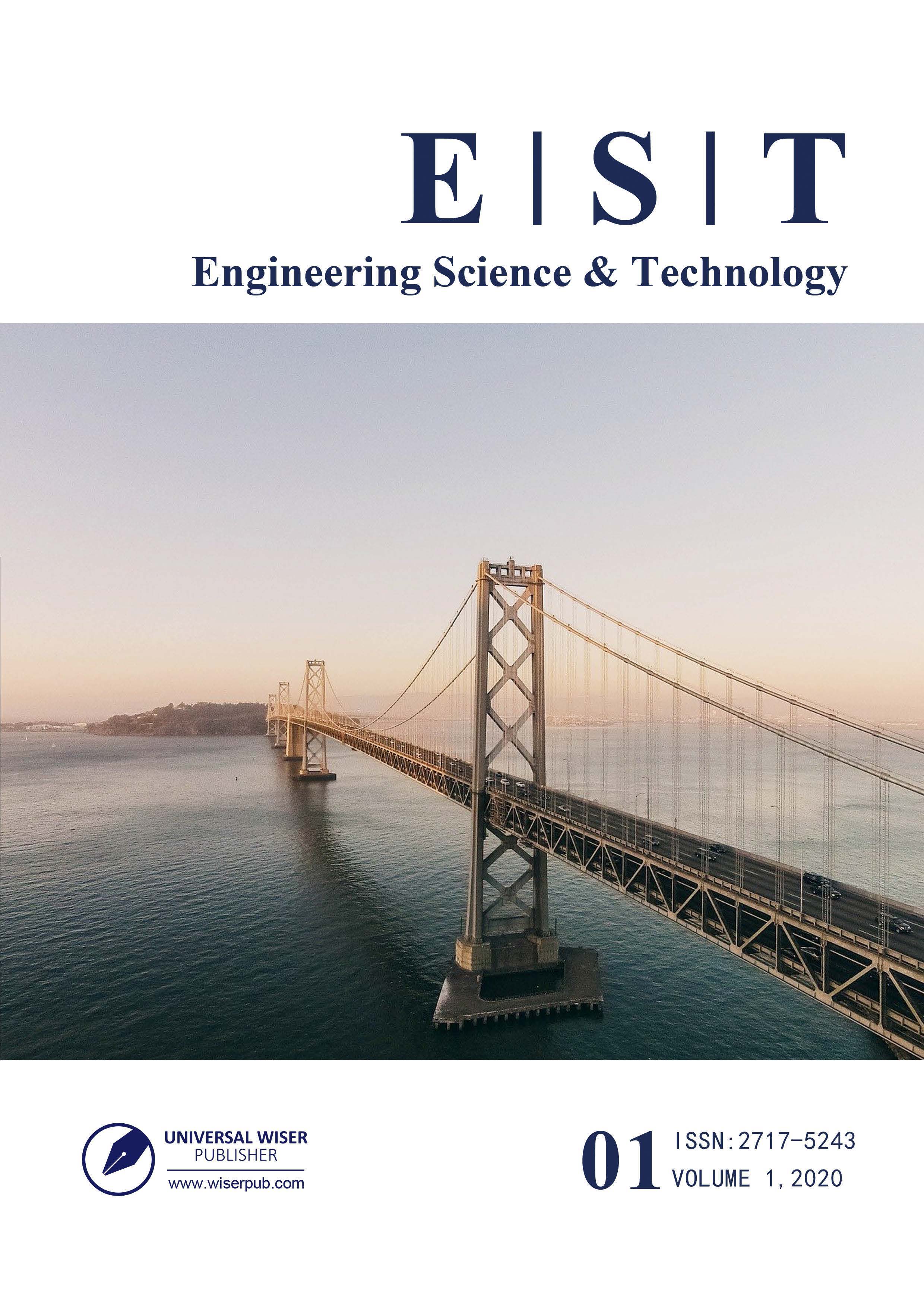
Downloads
Published
How to Cite
Issue
Section
License
Copyright (c) 2019 Engineering Science & Technology

This work is licensed under a Creative Commons Attribution 4.0 International License.